In the field of material science and engineering, metallography plays a crucial role in understanding the microstructure and properties of metallic materials. To obtain accurate and reliable results, scientists and researchers heavily rely on advanced metallographic equipment for specimen preparation. These cutting-edge tools have revolutionized the way metallography is conducted, enabling more precise analysis and enhancing the overall efficiency of the process. Metallographic Specimen Preparation involves several intricate steps, including cutting, mounting, grinding, polishing, and etching. Each stage requires careful attention to detail to ensure the preservation of the sample's original microstructure. With the advent of modern metallographic equipment, these processes have become more streamlined, accurate, and time-efficient. One of the most significant advancements in metallographic equipment is the development of automatic cutting machines. These machines utilize advanced technologies such as abrasive cutting, precision slicing, and water jet cutting to precisely section the metallic samples. The automatic cutting machines not only improve the accuracy of the cuts but also reduce the risk of human error, thus enhancing the reliability of the subsequent analysis. After cutting, the next crucial step is mounting the sample for further preparation. Traditional methods involved the use of thermosetting resins or cold mounting resins, which required time-consuming manual procedures. However, modern metallographic equipment has introduced automatic mounting machines that utilize hot compression mounting techniques. These machines ensure uniform and bubble-free mounting, eliminating the risk of introducing artifacts during the process. Grinding and polishing are essential steps in metallographic specimen preparation, as they help reveal the true microstructure of the material under investigation. In the past, manual grinding and polishing methods were labor-intensive and often resulted in uneven surfaces. Thanks to advanced metallographic equipment, automated Grinding And Polishing Machines have become commonplace. These machines employ precise control systems to ensure consistent pressure, speed, and direction during the process, resulting in highly polished surfaces with minimal deformation. Etching is another critical step in metallography, where chemicals are used to reveal the grain boundaries and other microstructural features. Traditional etching methods involved manual application of etchants, which often led to inconsistent results. However, the introduction of automatic etching machines has revolutionized this process. These machines provide precise control over the etching parameters, such as temperature, time, and concentration, ensuring consistent and repeatable results. Furthermore, modern metallographic equipment incorporates advanced imaging techniques for enhanced analysis. High-resolution optical microscopes with integrated digital cameras allow researchers to capture detailed images of the metallographic specimens. These images can be further analyzed using image analysis software, enabling quantitative measurements of grain size, phase distribution, and other microstructural features. Such advancements have significantly enhanced the accuracy and efficiency of metallographic analysis, enabling researchers to gain deeper insights into the materials being studied. In addition to the advancements in individual equipment, the integration of various metallographic equipment into comprehensive systems has further streamlined the specimen preparation process. These integrated systems allow for seamless transition between different preparation steps, reducing the overall time required for analysis. Moreover, data management software enables efficient organization, storage, and retrieval of the obtained results, enhancing the overall productivity and reproducibility of metallographic studies. The impact of these advancements in metallographic equipment extends beyond the realm of scientific research. Industries such as automotive, aerospace, and manufacturing heavily rely on metallography to ensure the quality and reliability of their products. The ability to accurately analyze the microstructure of metallic materials enables these industries to detect defects, assess material properties, and optimize manufacturing processes. Consequently, the advancements in metallographic equipment have played a pivotal role in enhancing the safety, performance, and longevity of various products and structures. In conclusion, metallographic equipment has undergone significant advancements in recent years, revolutionizing the way metallographic specimen preparation is conducted. From automatic cutting machines to integrated systems with advanced imaging and analysis capabilities, these tools have enhanced the accuracy, efficiency, and reliability of metallographic analysis. With these cutting-edge technologies at their disposal, scientists, researchers, and industries can gain a deeper understanding of metallic materials, leading to improved product quality, performance, and innovation.
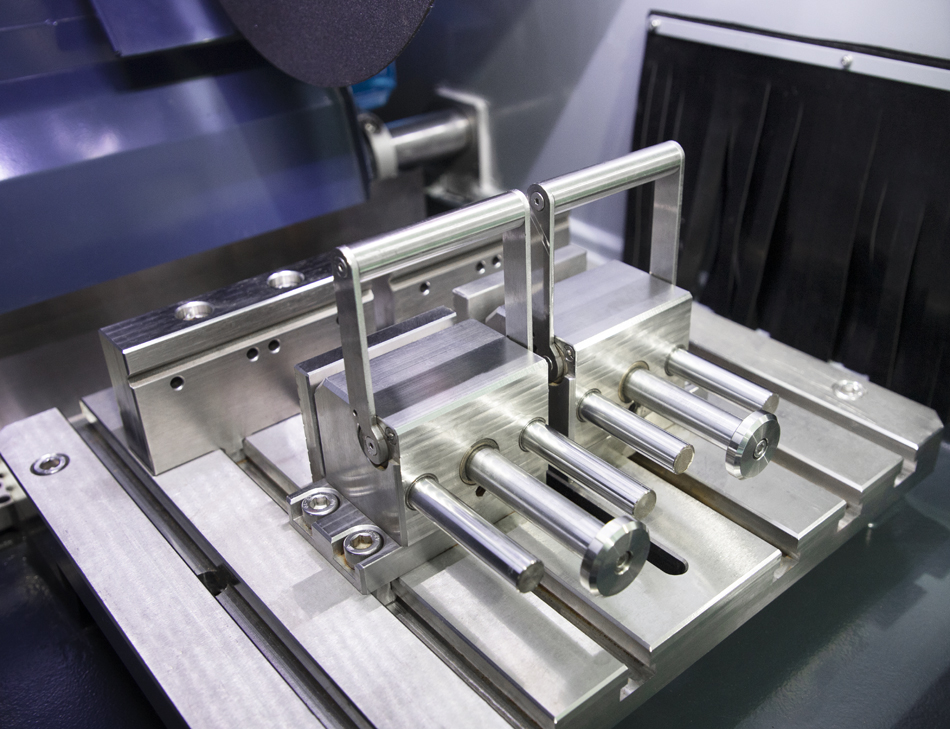